Demir Çelik Sektöründe Temiz Üretim Yaklaşımıyla Kaynak Verimliliği Uygulamaları
Özgen KÜÇÜKİL
Uzman
Yeşil Büyüme Politikaları Birimi
ozgen.kucukil@izka.org.tr
Ülkemizin lokomotif sektörlerinden biri olan demir çelik sektörü, başta inşaat olmak üzere her türlü makine-ekipman imalatı, otomotiv ve motorlu taşıt sektörleri gibi sanayinin birçok alanına girdi sağlarken, sanayileşmede diğer sektörlere yön verme özelliğine sahiptir. Sektörün üretim kapasitesi giderek artmakta ve ülkemiz 2019 yılı itibariyle dünyada 8. sırada, Avrupa’daki çelik üreticileri arasında ise Almanya’dan sonra 2. sırada yer almaktadır. Türkiye’de bulunan 70 adet demir çelik üretim tesisinin 8 tanesi İzmir’de bulunurken, ülkemizdeki en yüksek kapasiteli 11 üretim tesisi arasında yer alan 2 milyon tonu aşkın kapasiteleri ile HABAŞ ve Ege Çelik fabrikaları da İzmir’de faaliyet göstermektedir. Sektör özelinde her geçen gün yeni yatırım kararları alınmakta ve ana metal sanayi sektörünün ticaret hacminde artış yaşanması hedeflenmektedir [1].
Endüstriyel demir çelik üretim tesislerinin üretim safhaları, her bir aşamanın kendi alt üretim adımlarının olduğu çoklu proseslerden oluşmaktadır. Çelik üretiminin birden fazla yöntemi olmakla birlikte ağırlıklı olarak bazik oksijen fırını (BOF) ve elektrik ark ocağı (EAO) ile üretim yapılmaktadır. Hammadde olarak demir cevheri veya hurda kullanılmakta olup üretim yöntemleri hammadde kullanımına göre belirlenmektedir. Tek tip üretim yönteminin olmaması ve üretimin birden fazla aşama içermesi nedeniyle karmaşık yapıda bir üretim alanı olduğu söylenebilir. Temel üretim yöntemlerin yer aldığı safhalar aşağıdaki şemada gösterilmiştir:
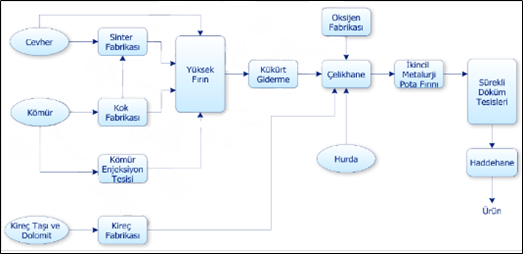
Enerji kullanımının yoğun olduğu demir çelik sektörünün Türkiye’nin toplam enerji tüketimi içerisindeki payı %7,5 iken sanayi tüketimi içerisindeki payı %21’dir. Sektör özelinde, enerjinin girdi maliyetlerindeki payı ise hammaddeden sonra 2. sırada yer almakta ve % 15-25 civarında yüksek bir orana karşılık gelmektedir [2]. Enerjiye ek olarak üretim esnasında çok fazla suyun da kullanıldığı, üretim sonucu çeşitli kirleticilerin açığa çıktığı ve meydana gelen emisyon oranının yüksek olduğu söylenebilmektedir. Üretimin her bir aşamasının girdi ve çıktı düzeyinde oluşturduğu çevresel etkiye yönelik hazırlanan tablo aşağıda sunulmuştur:
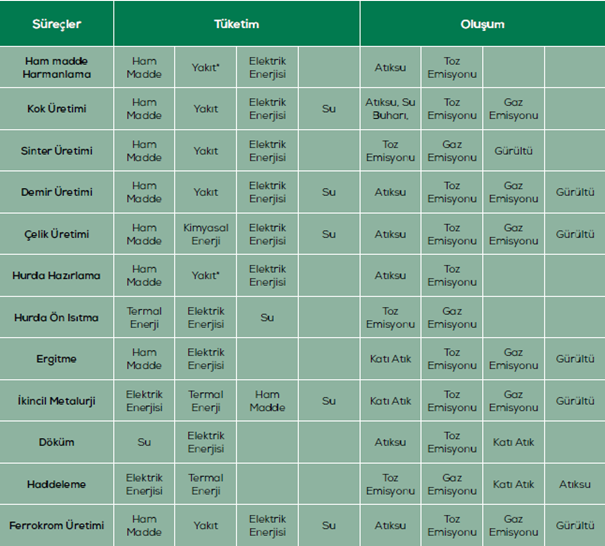
Tablodan da görülebileceği üzere, üretimin her aşamasında çeşitli çevresel etkiler oluşmakta, üretimin karmaşık yapıda olması ve çok aşamadan oluşması nedeniyle temiz üretim yaklaşımıyla tasarruf uygulamalarının yapılması için ciddi çalışmalar gerekmektedir. Uygulanabilecek tasarruf yöntemlerine kaynak ve atık türlerine göre kısaca değinilmiştir:
- Su tüketimi
Entegre demir çelik üretim tesislerinde kullanılan su miktarının büyük çoğunluğu soğutma ve temizlik amaçlı kullanılmaktadır. %55’lik bir oranla en fazla çelik üretimi sırasında kullanılan su, bu aşamada ocakların soğutulması ve döküm sonrası soğutma işleminin uygulanması sırasında sarf edilmektedir. Yüksek sıcaklıklarda işlemlerin gerçekleştirildiği ve çok miktarda suyun kullanıldığı bu sektörde, suyun tasarrufunun sağlanabilmesi için suyun devir daim edilerek kullanılması ile %98 oranında, kapalı devre sistemlerin kullanılması ile buharlaşma kayıpları azaltılarak %40 oranında su tasarrufu yapılabilmektedir [4; 3].
Yalnızca proses bazında su tüketiminin izlenmesi ve kontrolü yöntemiyle proses suyu tüketiminde %3-5, atık su miktarlarında %3-6, enerji tüketiminde %3-6, kimyasal tüketiminde %2-5, atık gaz emisyonlarında %3-6 ve katı atık miktarlarında %5-10 oranında tasarruf sağlanabilmektedir [10; 9].
2. Enerji tüketimi
Üretim sırasında enerji tüketiminde tasarruf edilebilmesi için dikkat edilmesi gereken öncelikler aşağıda belirtilmiştir:
- Tesis içerisinde etkin bir enerji yönetim sisteminin oluşturulması ve enerji tüketimlerinin takibinin yapılması,
- Soğutma amacıyla kullanılan suyun miktarını azaltmak için kuru soğutma sistemlerinin yaygınlaştırılması ve böylece enerjiden de tasarruf sağlanması,
- Her bir prosesin enerji tüketimini kontrol etmek için raporlama ve analiz araçlarının (Pinch Analizi, PUKÖ döngüsü vb.) kullanılması,
- Brülör ve tav fırınlarında yanma verimliliklerinin ve emisyonların kontrol edilmesi,
- Yakıt-hava oranının takibinin sağlanması ve optimizasyonu,
- Tesisteki önemli enerji akışları ve yanma prosesleri için çevrimiçi izleme – kontrol sistemlerinin kullanılması,
- Proses kontrolünün sağlanabilmesi için otomasyon sistemlerinin uygulanması,
- Reaktif gücün boyutunu azaltmak amacıyla alternatif akım (AC) devresinde kapasitörlerin kurulması,
- Hurda içeriğinin satın alma aşamasından itibaren takip edilerek hurdaların sınıflandırılması ve istenen çelik kalitesine göre kullanılması [2].
Üretim esnasında enerji verimliliğinin sağlanabilmesi için ilk olarak üretimde kullanılan tüm makine ve ekipmanların ısı yalıtımının çok iyi yapılması gerekmektedir. Böylelikle ısı kayıpları minimuma indirilecek ve düşük bütçeyle yüksek tutarlarda tasarruf sağlanabilecektir. Bir diğer dikkat edilmesi gereken unsur ise elektrik enerjisinden yararlanılan tesislerde kojenerasyon sistemlerinin kullanılmasıdır. Bu sayede hem yüksek oranda tasarruf sağlanacak hem de soğutma amaçlı enerji tüketiminde kojenerasyon sisteminde oluşan atık ısıdan faydalanılabilecektir.
Üretim aşamalarından olan ergitme, alaşımlama, tavlama ve koklaştırma işlemlerinin yüksek sıcaklıklarda gerçekleştirilmesi nedeniyle bu sıcaklıkların elde edilebilmesi için kullanılan enerji miktarı epey fazladır. Bu süreçte enerji elde edebilmek için kok fırın gazı, yüksek fırın gazı, doğal gaz ve kömür gibi çeşitli yakıtlar kullanılmaktadır [3]. Yakıt tüketiminde yakıt-hava oranının kontrol edilmesi ve optimizasyonunun sağlanması ile kazan veriminde %2-6 oranında enerji verimliliği sağlanabilmekte, oksijen tüketimi kontrol altına alınarak karbonmonoksit oluşumu da engellenebilmektedir [11, 12; 3].
Enerji verimliliğinin sağlanması açısından kontrol edilmesi gereken bir diğer unsur ise üretimde kullanılan motor güçlerinin üretim yüküyle paralel olarak seçilmiş olmasıdır. Daha düşük kapasitede çalıştırılan motorların enerji tüketimini arttırmaları nedeniyle yüksek verimlilik sağlayan motorların tercih edilmesi gerekmekte ve bu sayede enerji tüketiminde %1-3 oranında tasarruf sağlanabilmektedir [6; 3].
3. Atık su oluşumu
Demir çelik üretimi sonucunda ortaya çıkan atık suyun içerisinde çok fazla kimyasal ve fiziksel atık olması nedeniyle, atık su kullanılmadan önce mutlaka arıtma işleminden geçirilmesi gerekmektedir. Arıtıldıktan sonra sisteme sokularak tekrar kullanılan her litre atık su, üretimde kullanılan su miktarını da aynı ölçüde azaltmaktadır.
Demir çelik tesislerinin karmaşık üretim aşamalarından oluşması nedeniyle her aşama sonrası çıkan atığın karakteri de farklı olmaktadır. Bu nedenle üretim tesisi içerisinde atık suyun tekrar kullanılabilmesine yönelik olarak ilk yapılması gereken, her prosesten çıkan atık suyun kirlilik yüklerinin teker teker incelenmesi ve arıtma yönteminin belirlenmesidir.
Kok fırınından çıkan suyun içerisinde katran bulunması ve katranın tehlikeli bir madde olması nedeniyle, birden fazla aşamadan oluşan arıtma yöntemleri ile sudan ayrıştırılabilmektedir. Böylece buradan elde edilen su, sistemde kullanılmak üzere geri gönderilirken diğer yandan elde edilen katran çamuru da kok fırınında tekrar kullanılabilmektedir [4; 3].
4. Emisyonlar
Üretim sürecindeki temel emisyon kaynaklarından birisi hammadde, yardımcı madde, katkı maddeleri ve ürünlerin açıkta depolanması ve taşınması işlemleridir. Bu maddelerin açık alanlarda depolanması halinde rüzgâr etkisiyle tozuma oluşmakta ve bu oluşan tozlar tesis çevresini olumsuz yönde etkileyebilmektedir. Bu etki, malzemelerin yükleme-boşaltma ve taşınması sırasında daha da artmaktadır. Tozumanın azaltılması için malzemelerin kapalı alanlarda depolanması ve toz tutma sistemlerinin kullanılması gerekmektedir. Taşıma esnasında oluşacak toz emisyonlarının azaltılması için taşıma amaçlı konveyör bantların kullanılması, yolların sulanması ve temizliğinin sağlanması önemlidir [7].
Demir çelik üretimi aşamalarından olan kok üretimi aşaması, toz ve gaz emisyonunun yapıldığı aşamalardan biridir. Üretimin bu aşamasında toz, toplam organik karbon (TOK), benzen-toluen-ksilen (BTEX), uçucu organik bileşikler (UOB), hidrojen sülfür (H2S), SO2, amonyak (NH3), karbonmonoksit (CO), PAH (polisiklik aromatik hidrokarbon) ve cıva gibi ağır metaller salınmaktadır [4; 3]. Daha çok bacalardan havaya karışan bu maddeler, toz toplama ve fırın ısıtma sistemlerinden borular vasıtasıyla toplanan atık gaz içerisinde bulunmaktadır. Bu emisyonların torba filtre, elektrostatik filtre vb. gibi filtrasyon sistemleri kullanılarak azaltılması mümkündür. Fırın kapıları, valfler, şarj delikleri gibi alanlardan ve kok kömürü eleme aşamasında da fazla miktarda emisyon oluşmaktadır. Bu alanlar için de ıslak yıkama kuleleri kullanılabilmektedir [7].
Sinter üretim sürecinde ise tüm üretim sırasında yapılan emisyonun %50’sine karşılık gelen toz emisyonları oluşmakta ve uygun toz tutma sistemleriyle kontrol altına alınabilmektedir. Bununla beraber kurşun, cıva, çinko gibi ağır metal, demir bileşikleri, kurşun bileşikleri gibi partiküller, alkali klorürler, kükürt oksitleri, azot oksitleri, HCl (hidroklorik asit), HF (hidrojen florür), hidrokarbonlar, karbonmonoksit ile PAH, PCB (poliklorlu bifeniller) ve PCDD/F (Poliklorlu dibenzo-p-dioksinler ve poliklorlu dibenzofuranlar) gibi bileşiklerin de emisyonu yapılmaktadır [4; 3]. Bu toz emisyonlarının azaltılabilmesi için uygun yöntemler ve toz tutma sistemleri kullanılmalıdır [7].
5. Atık oluşumu
Sektörde üretim sonrasında yüksek fırın (YF) cürufu, çelik cürufu, toz, kömür külü gibi katı atıklar ortaya çıkmaktadır. Bu atıklardan en çok yüksek fırın cürufu inşaat sektöründe yol yapımı sırasında kullanılan hammaddeler arasına dâhil edilerek kullanılabilmektedir. Bir kısım cüruf ise tekrar çelik fırını içinde veya sinter tesisinde değerlendirilmektedir.
Gaz, toz ve çamur olarak oluşan atıkların neredeyse tamamının yeniden tesis içerisinde kullanılabilmesi, atık değerlendirmesine güzel bir örnek olmaktadır. Örneğin, kok fırını gazı %55 oranında hidrojen içermekte ve buradan elde edilen hidrojen gazı tesis içerisinde ihtiyaç duyulan enerjinin %40’ını karşılayacak ölçüde yeniden kullanılabilmektedir [8].
Kaynakça
- [1] Demir Çelik Sektör Raporu 2020, T.C. Sanayi ve Teknoloji Bakanlığı.
- [2] Sakarya O., Cengiz U., (2019). Türkiye Demir & Çelik İşletmelerinin Enerji Tasarrufu Potansiyeli, Bilecik Demir Çelik San. Tic. A.Ş, Türkiye.
- [3] Ana Demir ve Çelik Ürünleri ile Ferro Alaşımların İmalatı, Kaynak Verimliliği Rehberi, T.C. Sanayi ve Teknoloji Bakanlığı, 2019.
- [4] JRC, «Integrated Pollution Prevention and Control (IPPC) Reference Document Best Available Techiques (BAT) for Iron and Steel Production» 2013.
- [5] JRC, «Integrated Pollution Prevention and Control (IPPC), Reference Document on Best Available Techniques (BAT) for Ferrous Metals Processing Industry» 2001.
- [6] F. Dinçer, 2010. Asenkron Motorlar Enerji Verimliliği Çalışmaları ve Pratik Yaklaşımlar
- [7] Sanayiden Kaynaklanan Hava Kirliliğinin Belirlenmesi ve Azaltılmasına Yönelik Uygulamanın Kolaylaştırılmasının Sağlanması Projesi, 2019. Dokuz Eylül Üniversitesi ve T.C. Çevre ve Şehircilik Bakanlığı.
- [8] Öcal Y., (2014). Demir Çelik Sektöründe Atık Yönetimi, Uzmanlık Tezi, T.C. Kalkınma Bakanlığı.
- [9] Sanayide Temiz Üretim Olanaklarının ve Uygulanabilirliğinin Belirlenmesi Projesi, 2016. Çevre Ve Temiz Üretim Enstitüsü, TÜBİTAK.
- [10] Öztürk, E. (2014). Tekstil Sektöründe Entegre Kirlilik Önleme ve Kontrolü ve Temiz Üretim Uygulamaları. Fen Bilimleri Enstitüsü, Çevre Mühendisliği Anabilim Dalı, 518. Isparta: Süleyman Demirel Üniversitesi.
- [11] JRC, «Integrated Pollution Prevention and Control (IPPC), Reference Document on Best Available Techniques (BAT) for the Non-Ferrous Metals Industries» 2017.
- [12] A. Bilgin, «Kazanlarda Enerji Verimliliği» cilt 95, pp. 13-18, 2006.